In software development, the terms ‘Quality Assurance,’ and ‘Quality Control’ are often thrown around interchangeably. But it’s important to understand that Quality Assurance VS Quality Control (QA VS QC) are distinct concepts that form different parts of the quality management cycle. In this blog, we delve into the significance of these three terms and explore how they can be utilized to enhance the quality of a product.
This blog discusses the differences between Quality Assurance VS Quality Control. These are all essential parts of ensuring software works well, so understanding how they work together is vital if you want a great product. We’ll look at these processes and explain what makes them unique. If you’re into software testing or engineering or are just curious about software development, this blog will be super helpful! Let’s start exploring the world of Quality Control vs Quality Assurance !
Table Of Contents
- 1 Quality Assurance VS Quality Control (QA vs QC)- Overview
- 2 Quality Control and Quality Assurance: Origin
- 3 What are the Similarities Between Quality Assurance and Quality Control?
- 4 Does Quality Assurance Remove the Need for Quality Control?
- 5 QA vs QC – Real-life Scenario Examples
- 6 Quality Control: What Role Do Quality Audits and Inspection Play in Product Development?
- 7 Quality Assurance VS Quality Control (QA Vs QC)
- 8 Finally, What is the Relationship Between QA and QC?
- 9 Key Takeaways
- 10 Frequently Asked Questions
Quality Assurance Vs Quality Control (qa Vs QC)- Overview
What is Quality Assurance?
Quality assurance is “A system for evaluating performance, as in the delivery of services or the quality of products provided to consumers, customers, or patients.
“Quality Assurance(QA) is a standard process set up by an organization to meet quality standards. This process helps to avoid mistakes and defects, delivering products and services to customers.
QA is the foundation pillar for quality management as it focuses on the integrity of the product. It also provides confidence to stakeholders that desired and mentioned requirements are fulfilled.
What is Quality Control?
Quality Control is “setting standards and testing to ensure something, like a product or service, is done correctly.”
Quality control aims to check whether the prescribed model was followed. It can be achieved by performing audits and determining whether the team followed the defined model to attain quality.
Read More: Quality Assurance VS Testing
Quality Control and Quality Assurance: Origin
Both Quality Assurance and Quality control are interrelated. They are essential parts of quality management protocols followed by an organization. Initially, Quality control started to be followed in the 1920s by the manufacturing industry.
Quality control guidelines need to be implemented as the manufacturing industry demands the exact replicas of the original product in bulk without any variations. The Quality control process helps them check if the desired requirements were met without committing any mistakes.
With passing years, more research work and Growing technology made the manufacturing process more complex. This made the Quality control process even more complex.
This made the organization define a proper quality control process and ensure it is followed throughout that particular unit’s development.
In the 1950s, Quality Control was further extended in the manufacturing unit by performing Quality Assurance checks and Audits. The significant focus areas were the sectors related to public health and safety.
The idea behind “Assurance” was randomly selecting any manufactured piece from the batch and checking if it meets the desired requirement. If the piece is found to meet the requirement, it is passed.
It may be passed if the piece does not match the exact requirement but is within the defined range. If it is found out of the defined range, it has to be rejected and can lead to the immediate stopping of the manufacturing process and starting it all over again from scratch leading to loss of money and time. Because bulk manufacturing relies heavily on complex machinery, maintaining strict maintenance and inspection routines is essential to prevent unexpected. A heavy equipment maintenance app supports this by helping schedule and track maintenance activities, ensuring equipment reliability and enabling audits to confirm adherence to quality standards throughout the manufacturing process.
Quality control focuses on auditing the project and checking if defined guidelines and protocols were followed while manufacturing.
What Are the Similarities between Quality Assurance and Quality Control?
Quality assurance (QA) and quality control (QC) are integral components of a comprehensive quality management system. Despite their distinct roles, they share several similarities:
- Focus on Quality: Both QA and QC aim to ensure the quality of products, services, or processes. While QA prevents defects by establishing and implementing processes and standards, QC focuses on identifying and correcting defects through inspection, testing, and analysis.
- Customer Satisfaction: Both QA and QC ultimately aim to satisfy customer requirements and expectations. Maintaining high-quality standards and delivering defect-free products or services contribute to customer satisfaction and loyalty.
- Continuous Improvement: Both QA and QC emphasize the importance of continuous improvement. QA involves establishing processes for ongoing enhancement of quality management practices, while QC involves identifying areas for improvement based on defects found during inspection or testing.
- Data-Driven Approach: QA and QC use data and metrics to assess quality. QA uses data to establish quality standards, measure process performance, and identify areas for improvement. QC uses data from inspections, tests, and analysis to identify defects and make informed decisions about corrective actions.
- Interdependence: QA and QC are interdependent and complementary functions. While QA sets the foundation for quality by establishing processes and standards, QC ensures these standards are met through inspection and testing. Feedback loops between QA and QC enable continuous improvement by incorporating insights and lessons learned from each function.
- Documentation: QA and QC require proper documentation to ensure traceability and accountability. QA documentation includes quality plans, procedures, and standards, while QC documentation includes inspection reports, test results, and corrective action records.
- Employee Involvement: Both QA and QC require the involvement and commitment of employees at all levels of an organization. Employees contribute to QA by adhering to established processes and standards and participating in continuous improvement initiatives. In QC, employees are responsible for conducting inspections, tests, and analysis to ensure product or service quality.
Does Quality Assurance Remove the Need for Quality Control?
The question of whether Quality Assurance (QA) eliminates the need for Quality Control (QC) is a common one in quality management. While QA establishes strong foundations, QC remains essential for several reasons.
Almost up to 90% of companies implement QA and QC for optimal quality management.
Quality Assurance VS Quality Control : A Proactive & Reactive Partnership
- Focus: QA is proactive, preventing defects by establishing processes, policies, and standards. QC is reactive, meticulously ensuring adherence to established guidelines and identifying any issues that may have slipped through.
- Timing: QA is implemented throughout a project’s lifecycle, while QC often occurs after specific stages or at project completion.
- Analogy: Think of QA as designing a building’s blueprints and QC as inspecting the construction to ensure it follows the plans.
The Work of QA and QC
QA creates a framework for achieving quality, but it’s QC that actively measures and verifies its effectiveness. The results of QC can then be fed back into QA to refine processes for future projects.
Imagine QA setting the processes and QC checking the deliverable to ensure it meets expectations.
Real-World Example:
Software Development:
QA defines bug reporting standards in software testing, while QC executes those standards by testing the application and logging bugs according to the defined format.
QA can update the standards to improve future bug reports if QC identifies a need for additional information (e.g., a probable root cause).
QA Vs QC – Real-life Scenario Examples
Let’s delve deeper into the software development scenario we described in the previous section, highlighting the interplay between QA and QC:
QA Sets the Stage for Effective Bug Reporting
Imagine the QA team is building the foundation for quality bug reports. They establish clear guidelines outlining the information testers must capture when encountering issues. These guidelines, essentially the QA standards, might specify details like:
- Summary: A concise description of the bug (e.g., “Login button not working”).
- Steps to Reproduce: Detailed instructions on consistently triggering the bug (e.g., “1. Navigate to the login page. 2. Enter valid username and password. 3. Click the login button.”).
- Expected Result: What should happen under normal circumstances (e.g., “User is redirected to the dashboard.”).
- Actual Result: The behavior observed that indicates a bug (e.g., “Nothing happens when clicking the login button.”).
- Optional: Additional sections like screenshots or error messages can also be included in the standards.
QC Puts the QA Standards Into Action
The QC team, acting as the testers, then executes these predefined standards during the software testing phase. They meticulously test the application, logging any bugs they encounter. While following the QA guidelines, they fill out the bug report template, ensuring all necessary information is captured for clear and actionable reports.
QC Identifies Room for Improvement
Here’s where the true work between QA and QC comes into play. Let’s say the QC team encounters a bug where the menu bar disappears when scrolling down a webpage. They can successfully document the issue using the existing QA standards (summary, steps to reproduce, expected result, actual result).
Yet, the QC team might identify a gap in the standards. For example, the report might lack information about the “expected result” under normal circumstances (i.e., the menu bar should remain visible).
QA Adapts & Improves Based on QC Feedback
This valuable insight from QC feeds back into the QA process. Recognizing the need for a more comprehensive report, the QA team can update the bug reporting standards.
They might add a mandatory field for “expected result,” ensuring all future reports clearly outline what the normal behavior should be.
This continuous improvement loop, fueled by QC’s findings, strengthens the overall quality of bug reporting.
Benefits of Collaboration
This example showcases the beautiful collaboration between QA and QC. QA establishes a systematic approach to bug reporting, and QC meticulously implements it. By identifying areas for improvement in the reporting process, QC empowers QA to refine the standards, leading to more detailed and actionable bug reports.
Ultimately, this teamwork benefits the entire development process by ensuring clear communication of issues and facilitating faster resolution of bugs.
Quality Control: What Role Do Quality Audits and Inspection Play in Product Development?
Quality Audits are the onsite evaluation of a process to ensure compliance with the requirements. They are performed under the supervision of an auditor who checks whether set guidelines were practiced during the making of the product.
Audits are not about checking the product quality but about inspecting the type of work done in making a product. It evaluates how closely the prescribed model was followed. Are there any variations? If yes, then what is the reason behind variations?
The objective of audits is to continuously improve the quality of the work henceforth increasing product quality. Inspection can be one of the aspects of an Audit.
The inspection examines the traits of a product. It checks how well the product fits requirements and whether there are any variations between the developed product and desired product. If yes, will it fit the requirement or not? How many can load/stress products handle? Which adverse situation can make it crash?
In short, the audit examines the quality of the process used while making a product. Inspection is about examining how well the product fits the requirement provided by stakeholders.
Quality and inspection are practiced in various industries, such as software, manufacturing, automobile, retail, etc., to ensure all follow a standard procedure and practice.
As in bulk manufacturing, any deviation from the standard procedure might lead to mistakes, resulting in the loss of a considerable amount of money and time.
Quality Assurance Vs Quality Control (qa Vs QC)
One focuses on finding and fixing mistakes, and the other makes sure that mistakes don’t happen in the first place; many differences make these two stand apart, and let’s take a look at the differences between Quality Control and Quality Assurance:
Feature | Quality Assurance (QA) | Quality Control (QC) |
Goal | To detect and prevent defects throughout the development process | To identify and fix defects in a product after the development cycle |
Approach | Proactive | Reactive |
Objective | Assures that the quality requested by the customer will be achieved | Focuses on fulfilling the quality requested |
Activities | Process improvement, test planning, reviews | Test execution, defect reporting |
Team | The entire development team and other team members involved in product development | Testing team |
Process/ Product-oriented | It is process-oriented as it focuses on maintaining QA processes to ensure consistent quality throughout product development. | It is product-oriented and consists of activities that evaluate the quality of products. |
Focus | High-quality software development process | High-quality software product |
Standards | Defines standards and methodologies to meet customer requirements | Ensures adherence to standards while working on the product |
Involved in which stage of SDLC? | Throughout the development lifecycle | After the development and testing stages |
Measure | Effectiveness of defect prevention | Number of defects identified |
Techniques | A preventive technique that manages the product’s quality | A corrective technique that evaluates the product’s quality |
Emphasis | Customer or User | Standard |
Order of execution | Performed before QC | Performed after QA |
Type of tool | Managerial tool | Corrective tool |
Activity level | It is a low-level activity that identifies defects that QC can not | It is a high-level activity that identifies defects that escape even after QA |
SDLC/STLC | It is responsible for the entire software development lifecycle | It is responsible for the entire software testing lifecycle |
Time consumption | It is a less time-consuming activity | It is a highly time-consuming activity |
Outcome | Prevents defects using robust QA processes | Ensures defects that occur after release are caught and corrected |
Statistical technique | Statistical Process Control (SPC) is the statistical technique applied to QA | Statistical Quality Control (SQC) is the statistical technique applied to QC |
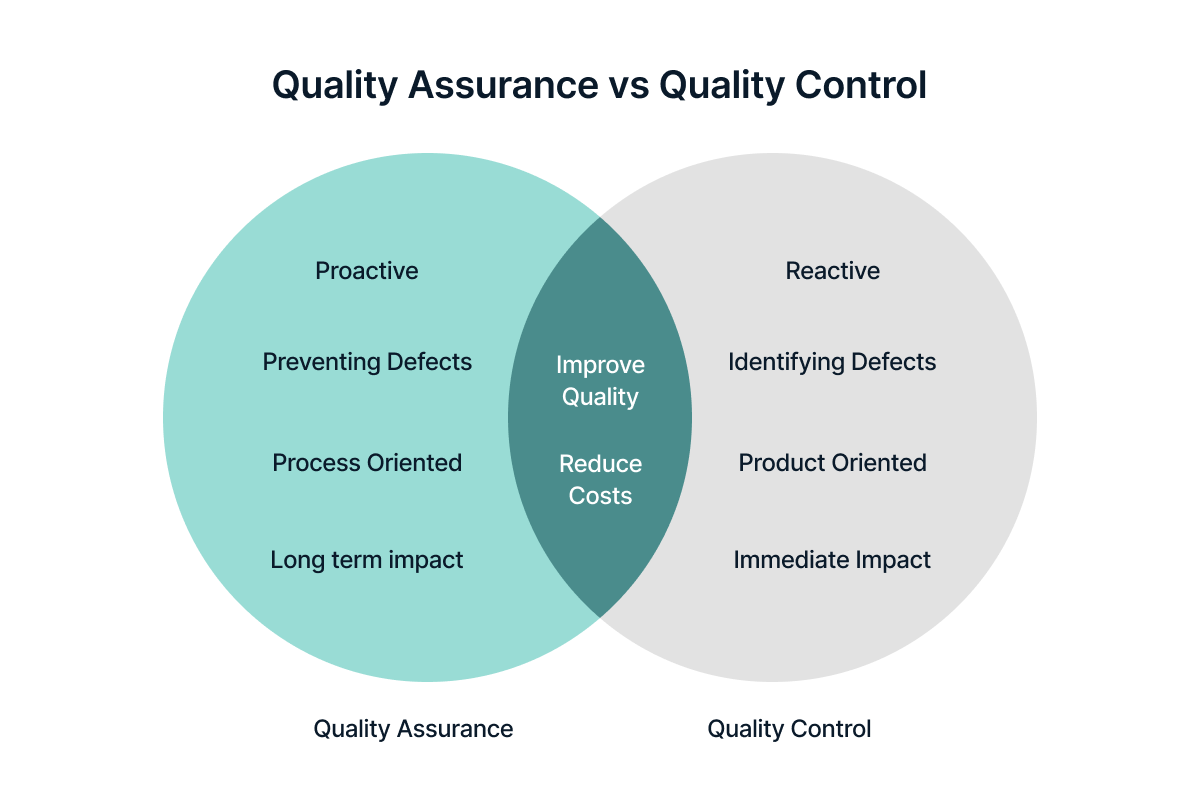
Finally, What is the Relationship between QA and QC?
QA, QC, are like a chain that works together to ensure a high-quality product. QA sets the standards for how it should be done, QC ensures those standards are followed, checks that everything is up to the quality standards. That way, any issues can be found quickly so they can be fixed before anyone else sees them.
QA, QC, are all crucial steps to make sure that a product is up to the standard it should be. Testsigma can help you to get precisely what you want. It’s a cloud-based testing solution that automates the testing process, so you don’t have to do it manually and waste time. It also provides a Quality Control environment to ensure everything is done right and the product is top-notch. So if you’re a software tester or quality assurance engineer, TestSigma is perfect for you! Get started and see how it can improve your software testing process and product quality.
Key Takeaways
Every company aims to deliver products with exceptional quality and user experience to customers. How can one achieve that? Quality Assurance and Quality Control are the processes that help businesses follow high standards in product development to deliver outstanding quality. Striking the right balance between QA and QC is essential to ensure product quality and mitigate risks.
Frequently Asked Questions
Quality Assurance (QA) comes first as QA testers help identify bugs during the development cycle, while the Quality Control (QC) team helps identify and fix bugs that exist after the development.
No, QC is not a part of QA. They are different teams that complement each other and contribute to the overall quality management of the product.
No, QC can not be achieved without QA. They rely on each other to be effective. QA comes first and then comes QC. QA helps prevent bugs during development, while QC identifies and fixes bugs after development. Overall, they help maintain and improve the quality of the products.